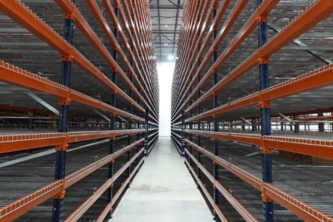
Case Study - Municipal Record Storage
A large Atlanta area government municipality realized they could no longer rely on their current storage buildings to continue to adequately service the surrounding community...
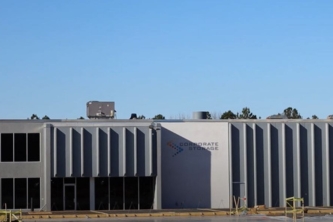
Case Study - Corporate
Storage
Corporate Storage is a third-party logistics company offering secured dry storage, climate-controlled storage, flexible spaces, and barcode-tracked storage in North Georgia...
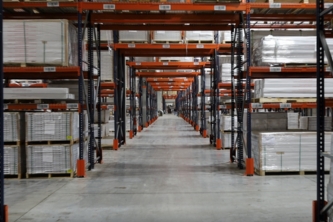
Case Study - QEP
Company
Earlier in 2022, QEP Company needed someone to help them take on an especially large pallet racking project. QEP Company brought in McGee Storage & Handling to...
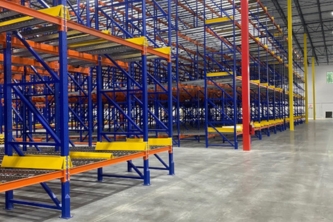
Case Study - Piedmont Healthcare
Piedmont Hospital has been in existence since 1905 and has represented a stable, prominent reputation as one of Atlanta’s premier health care providers. McGee...
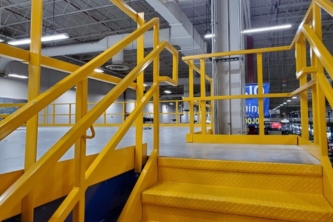
Case Study -Yamaha Motor Sports
When it comes to expanding a work area, some might expect for the plan to include building out, increasing the overall surface area of a space. However, embracing...
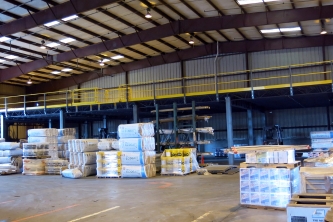
Case Study - Capitol Materials
McGee Storage and Handling joined forces with several contractors to help Capitol Materials expand their space with mezzanines while staying in code with the city...